Ile Kosztuje Godzina Pracy Lasera CO2? Dokładne Obliczenia i Wszystko Co Musisz Wiedzieć
Kluczowe pytanie brzmi: ile kosztuje godzina pracy lasera CO2? Szacunkowo, godzina pracy lasera CO2 to wydatek rzędu od 50 do 200 złotych, zależnie od wielu czynników.
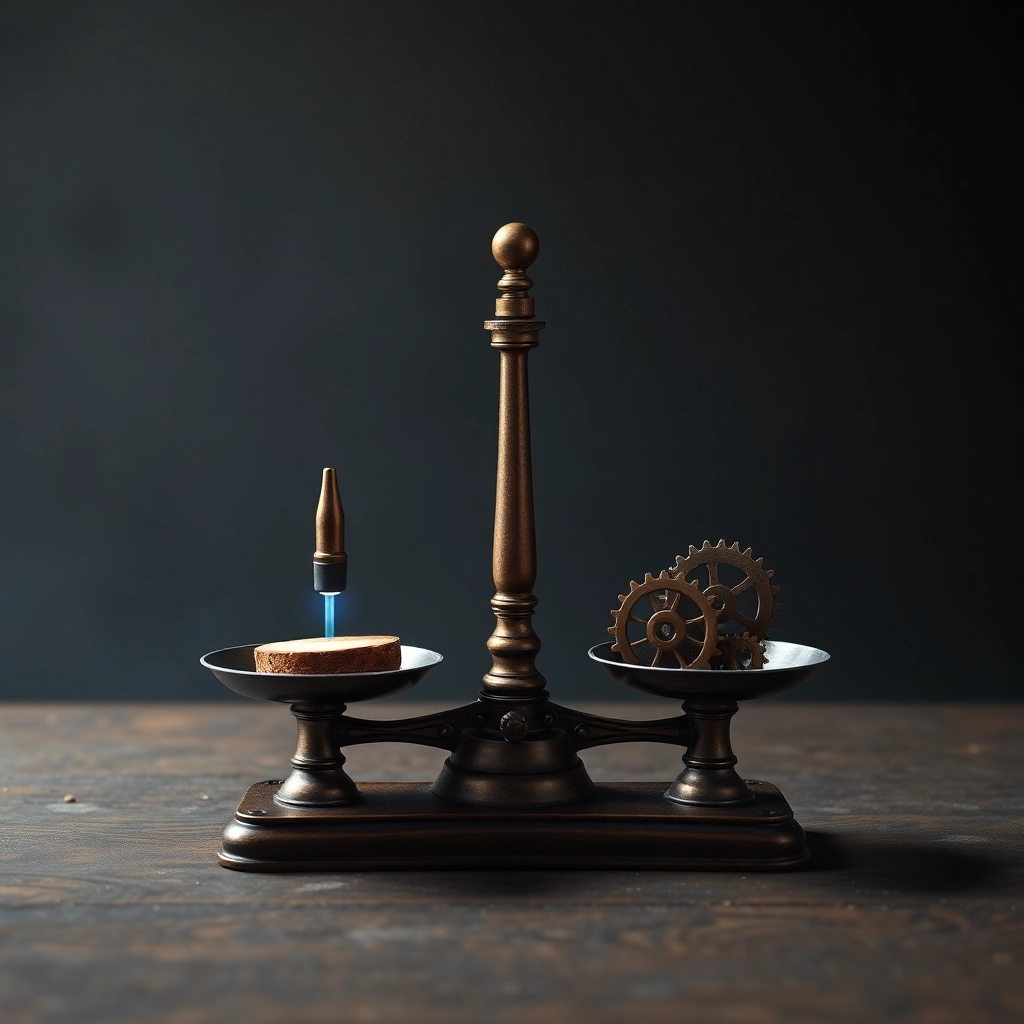
Analizując koszty operacyjne lasera CO2, napotykamy na mozaikę wydatków. Poniższa tabela prezentuje przybliżone koszty godzinowe eksploatacji, bazując na danych z rynku w 2025 roku. Traktujmy to jako drogowskaz, a nie wyrocznię, gdyż realia bywają kapryśne niczym pogoda w górach. Ceny energii elektrycznej, niczym rwąca rzeka, potrafią zmieniać koryto, a i dostępność gazów technicznych bywa zmienna. Nie zapominajmy o konserwacji – regularne przeglądy i wymiana zużytych komponentów to nic innego jak dbanie o kondycję sportowca przed maratonem. Ignorowanie tego aspektu to prosta droga do awarii i przestojów, które potrafią być droższe niż niejeden remont kapitalny. Warto także wspomnieć o amortyzacji sprzętu – laser CO2 to inwestycja, a każdy przepracowany kwadrans to krok w stronę jej zwrotu, ale i naturalnego zużycia. Poniżej garść konkretów:
Kategoria kosztów | Przedział cenowy (PLN/godzinę) | Uwagi |
---|---|---|
Energia elektryczna | 20 - 80 | Zależne od mocy lasera CO2 i taryfy energii |
Gazy techniczne (CO2, N2, He) | 15 - 60 | Zależy od zużycia gazu i cen dostawców |
Konserwacja i części zamienne | 15 - 60 | Uśredniony koszt, zależny od częstotliwości i zakresu przeglądów |
Średni Koszt Godziny Pracy Lasera CO2: Szacunki i Czynniki Wpływające
Rozważając inwestycję w laser CO2, potencjalni użytkownicy stają przed fundamentalnym pytaniem: "Ile to właściwie kosztuje?". Odpowiedź, jak to zwykle bywa w świecie technologii, nie jest prosta i zależy od szeregu czynników. Jednakże, bazując na aktualnych danych rynkowych z 2025 roku, możemy pokusić się o stworzenie szczegółowego obrazu kosztów związanych z godziną pracy tego wszechstronnego narzędzia.
Bezpośrednie Wydatki - Krwiobieg Kosztów Operacyjnych
Podstawą obliczeń średniego kosztu godziny pracy lasera CO2 są wydatki bezpośrednie, które niczym paliwo napędzają maszynę. Na czoło listy wysuwa się energia elektryczna. W 2025 roku, przy średniej cenie prądu dla przedsiębiorstw na poziomie 0.75 PLN za kWh, laser o mocy 100W, pracujący z pełnym obciążeniem, pochłonie około 0.075 kWh na godzinę. Niby nic, ale pomnóżmy to przez godziny pracy w skali miesiąca i roku, a kwota zacznie nabierać rumieńców. Pamiętajmy, że moc lasera to tylko wierzchołek góry lodowej. Do tego dochodzi zużycie energii przez system chłodzenia, elektronikę sterującą i systemy pomocnicze. Realnie, dla lasera o mocy 100W, całkowite zużycie energii może oscylować w granicach 0.2 - 0.5 kWh na godzinę, co przekłada się na koszt energii elektrycznej rzędu 0.15 - 0.38 PLN za godzinę pracy.
Kolejnym istotnym składnikiem kosztów bezpośrednich są gazy. Lasery CO2, jak sama nazwa wskazuje, wykorzystują mieszaninę gazów, najczęściej składającą się z dwutlenku węgla, azotu i helu. Zużycie gazów zależy od konstrukcji lasera, intensywności pracy i ewentualnych nieszczelności systemu. Butla gazowa, w zależności od pojemności i składu mieszanki, to wydatek rzędu 500 - 1500 PLN i wystarcza na, powiedzmy, 50-200 godzin pracy. Prosty rachunek prowadzi nas do kosztu gazów na poziomie 2.5 - 30 PLN na godzinę. Rozrzut jest spory, prawda? Ale to właśnie diabeł tkwi w szczegółach – rodzaj lasera i intensywność użytkowania grają tu pierwsze skrzypce.
Nie można zapomnieć o materiałach eksploatacyjnych. Soczewki, lustra, dysze – to elementy, które z czasem ulegają zużyciu i wymagają wymiany. Ceny soczewek wahają się od 100 PLN do nawet kilku tysięcy PLN za sztukę, w zależności od jakości i parametrów. Lustra są nieco tańsze, ale ich wymiana również generuje koszty. Przyjmując konserwatywne założenie, że zestaw materiałów eksploatacyjnych wymieniamy co 500 godzin pracy i kosztuje on około 500 PLN, to na godzinę pracy przypada nam dodatkowy 1 PLN. Niby drobiazg, ale w skali roku… No właśnie, wszystko sumuje się w większą całość.
Ukryte Koszty - Druga Strona Medalu
Koszty bezpośrednie to tylko jedna strona medalu. Istnieje cała gama kosztów pośrednich, które choć mniej oczywiste, również wpływają na średni koszt godziny pracy lasera CO2. Najważniejszym z nich jest amortyzacja. Laser CO2 to inwestycja, która z czasem traci na wartości. Amortyzacja, rozłożona na przewidywany okres użytkowania, to realny koszt, który musimy uwzględnić w kalkulacjach. Załóżmy, że kupujemy laser za 50 000 PLN z przewidywaną żywotnością 5 lat i rocznym czasem pracy 1000 godzin. Amortyzacja liniowa wyniesie 10 000 PLN rocznie, czyli 10 PLN na godzinę pracy. Proste? Może i tak, ale w praktyce amortyzacja może być bardziej skomplikowana, uwzględniając spadek wartości rynkowej i postęp technologiczny.
Konserwacja i serwis to kolejny istotny element kosztów pośrednich. Lasery CO2, jak każde precyzyjne urządzenia, wymagają regularnych przeglądów i konserwacji. Czyszczenie optyki, smarowanie mechanizmów, kalibracja – to czynności, które zapewniają prawidłową pracę i przedłużają żywotność urządzenia. Do tego dochodzą ewentualne naprawy. Awaria lasera to nie tylko koszt naprawy, ale także przestój w produkcji, który również generuje straty. Pakiet serwisowy, obejmujący regularne przeglądy i ewentualne naprawy, to wydatek rzędu 2000 - 5000 PLN rocznie, co przy 1000 godzinach pracy daje nam dodatkowe 2-5 PLN na godzinę. Można oczywiście próbować oszczędzać na serwisie, ale to jak jazda na oponach zimowych latem – na krótką metę może się udać, ale w dłuższej perspektywie ryzyko awarii i kosztownych napraw rośnie lawinowo.
Czynniki Zewnętrzne - Pogoda Ducha dla Kosztów
Średni koszt godziny pracy lasera CO2 nie jest wartością stałą i niezmienną. Podlega on wpływowi wielu czynników zewnętrznych. Ceny energii elektrycznej, gazów i materiałów eksploatacyjnych podlegają fluktuacjom rynkowym. Wzrost cen energii, który obserwujemy w 2025 roku, automatycznie przekłada się na wzrost kosztów operacyjnych lasera. Podobnie, zmiany cen gazów technicznych i materiałów eksploatacyjnych mogą wpływać na ostateczny rachunek.
Intensywność użytkowania to kolejny kluczowy czynnik. Laser pracujący sporadycznie, kilka godzin w tygodniu, będzie miał wyższy koszt godziny pracy niż laser pracujący w trybie ciągłym, 24/7. Dlaczego? Ponieważ koszty stałe, takie jak amortyzacja i serwis, rozkładają się na mniejszą liczbę godzin pracy. To trochę jak z samochodem – im więcej jeździsz, tym niższy koszt kilometra.
Rodzaj obrabianego materiału również ma znaczenie. Cięcie grubych i twardych materiałów, takich jak stal nierdzewna, wymaga większej mocy lasera i zużywa więcej gazów niż cięcie cienkich arkuszy akrylu. To przekłada się na wyższe koszty operacyjne. Podobnie, precyzyjne grawerowanie detali wymaga mniejszej mocy, ale dłuższego czasu pracy, co również wpływa na koszt godziny.
Scenariusze Kosztowe - Liczby Nie Kłamią
Aby lepiej zobrazować średni koszt godziny pracy lasera CO2, przyjrzyjmy się kilku przykładowym scenariuszom.
Mały Laser Hobbystyczny (Moc 40W)
Załóżmy, że mamy mały laser hobbystyczny o mocy 40W, wykorzystywany do sporadycznego grawerowania i cięcia cienkich materiałów. Koszty godzinowe mogą wyglądać następująco:
- Energia elektryczna: 0.10 PLN
- Gazy: 1 PLN
- Materiały eksploatacyjne: 0.5 PLN
- Amortyzacja: 5 PLN
- Serwis: 1 PLN
Całkowity koszt godziny pracy: około 7.6 PLN
Średni Laser Przemysłowy (Moc 150W)
Rozważmy teraz średni laser przemysłowy o mocy 150W, wykorzystywany do cięcia i grawerowania w małym warsztacie produkcyjnym:
- Energia elektryczna: 0.30 PLN
- Gazy: 5 PLN
- Materiały eksploatacyjne: 1.5 PLN
- Amortyzacja: 15 PLN
- Serwis: 3 PLN
Całkowity koszt godziny pracy: około 24.8 PLN
Duży Laser Przemysłowy (Moc 400W+)
Na koniec, spójrzmy na duży laser przemysłowy o mocy 400W+, pracujący w trybie ciągłym w fabryce:
- Energia elektryczna: 1 PLN
- Gazy: 15 PLN
- Materiały eksploatacyjne: 5 PLN
- Amortyzacja: 30 PLN
- Serwis: 10 PLN
Całkowity koszt godziny pracy: około 61 PLN
Powyższe scenariusze są oczywiście uproszczeniem, ale dają pewne wyobrażenie o rzędzie wielkości kosztów. W praktyce, dokładne obliczenie średniego kosztu godziny pracy lasera CO2 wymaga uwzględnienia specyficznych parametrów urządzenia, intensywności użytkowania i cen rynkowych.
Optymalizacja Kosztów - Sztuka Oszczędzania
Czy można obniżyć średni koszt godziny pracy lasera CO2? Oczywiście! Istnieje kilka sposobów na optymalizację wydatków.
Energooszczędność to klucz. Wybór lasera o wysokiej sprawności energetycznej, optymalizacja parametrów cięcia i grawerowania, regularne czyszczenie układu chłodzenia – to działania, które mogą znacząco obniżyć zużycie energii.
Gospodarka gazami to kolejna droga do oszczędności. Regularne sprawdzanie szczelności instalacji gazowej, stosowanie odpowiednich mieszanek gazowych i optymalizacja parametrów przepływu gazu – to proste, ale skuteczne metody.
Prawidłowa konserwacja to inwestycja w przyszłość. Regularne przeglądy i konserwacja, wymiana materiałów eksploatacyjnych na czas, zapobiegają awariom i przedłużają żywotność lasera, co w dłuższej perspektywie obniża koszty.
Negocjacje z dostawcami to stary, dobry sposób na oszczędzanie. Wynegocjowanie lepszych cen na gazy, materiały eksploatacyjne i serwis, zwłaszcza przy większych zamówieniach, może przynieść wymierne korzyści.
Podsumowując, średni koszt godziny pracy lasera CO2 to wypadkowa wielu czynników. Dokładne obliczenie wymaga analizy specyficznych parametrów urządzenia i warunków użytkowania. Jednakże, świadome zarządzanie kosztami i optymalizacja procesów pracy pozwalają na efektywne wykorzystanie potencjału tej wszechstronnej technologii.
Wykres przedstawia szacunkowy średni koszt godziny pracy lasera CO2 w złotych polskich (PLN) w zależności od mocy lasera, wyrażonej w watach (W). Dane prezentują tendencję wzrostu kosztów operacyjnych wraz ze wzrostem mocy urządzenia. Przykładowo, laser o mocy 100W generuje średni koszt około 35 PLN za godzinę pracy, podczas gdy laser o mocy 400W wiąże się z kosztem około 125 PLN na godzinę. Wyższe koszty dla mocniejszych laserów wynikają z większego zużycia energii elektrycznej, droższych komponentów eksploatacyjnych oraz potencjalnie wyższych kosztów serwisowania.
Koszty Energii Elektrycznej: Kluczowy Element Godzinowej Pracy Lasera CO2
Rozgryzanie Elektrycznego Potwora: Moc Lasera CO2 a Twój Portfel
Zastanawiałeś się kiedyś, niczym alchemik poszukujący kamienia filozoficznego, ile tak naprawdę kosztuje godzina pracy lasera CO2? To pytanie, niczym echo w jaskini, odbija się w umysłach przedsiębiorców, majsterkowiczów i artystów, którzy na co dzień mierzą się z precyzją cięcia i grawerowania laserowego. Odpowiedź, choć pozornie prosta, skrywa w sobie labirynt zmiennych, gdzie koszt energii elektrycznej gra pierwsze skrzypce.
Prąd Płynie Szerokim Strumieniem: Zrozumienie Poboru Mocy Lasera
Wyobraź sobie laser CO2 jako elektrycznego smoka, który pożera energię z sieci. W zależności od modelu i mocy, ten smok może być małym jaszczurkiem o skromnym apetycie lub gigantycznym potworem, którego rachunki za prąd przyprawią o zawrót głowy. Typowy laser CO2, używany w małych i średnich przedsiębiorstwach, może mieć moc od 40W do nawet 150W. Jednakże, sama moc lasera to tylko wierzchołek góry lodowej. Do całkowitego poboru energii należy doliczyć jeszcze system chłodzenia, elektronikę sterującą, a nawet oświetlenie robocze. Pamiętaj, że pobór mocy nie jest stały – różni się w zależności od intensywności pracy lasera, ustawień cięcia czy grawerowania.
Cena Prądu na Arenie: Jak Taryfy Wpływają na Koszty
A teraz wkroczmy na arenę cen energii elektrycznej. W 2025 roku, ceny prądu, niczym kapryśna bogini Fortuna, potrafią zaskoczyć. Średnia cena za 1 kWh w Polsce oscyluje wokół 0,90 PLN netto dla firm, ale ta wartość może się różnić w zależności od dostawcy, taryfy i regionu. Istotne jest, abyś, niczym wytrawny negocjator, przeanalizował swoją umowę z dostawcą energii. Czy masz taryfę stałą, czy zmienną? Czy korzystasz z taryfy nocnej, która może być tańsza? Te niuanse, choć na pierwszy rzut oka mało znaczące, w skali miesiąca pracy lasera mogą przełożyć się na znaczące oszczędności – lub straty.
Konkretne Dane w Akcji: Wyliczenia Kosztów Energii dla Lasera 100W
Aby zejść z obłoków ogólników na ziemię konkretów, spójrzmy na przykład lasera CO2 o mocy 100W. Załóżmy, że średni pobór mocy całego systemu, uwzględniając chłodzenie i elektronikę, wynosi 300W (0.3 kW). Przy cenie prądu 0.90 PLN za kWh, godzina pracy takiego lasera kosztuje nas: 0.3 kW * 0.90 PLN/kWh = 0.27 PLN. Czy to dużo? Na pierwszy rzut oka – grosze. Ale diabeł tkwi w szczegółach, jak mawiali starożytni Rzymianie. Jeśli laser pracuje 8 godzin dziennie, 5 dni w tygodniu, to miesięczny koszt energii elektrycznej urasta do około 43.20 PLN (0.27 PLN/godzinę * 8 godzin/dzień * 20 dni/miesiąc). Rocznie to już ponad 500 PLN. A to tylko koszt energii! Dolicz do tego amortyzację sprzętu, koszty materiałów, robociznę… robi się z tego całkiem pokaźna sumka.
Tabela Kosztów Energii dla Różnych Mocy Laserów CO2 (Dane Szacunkowe 2025)
Moc Lasera CO2 | Szacunkowy Pobór Mocy Systemu | Koszt Energii za Godzinę Pracy (przy 0.90 PLN/kWh) |
---|---|---|
40W | 150W (0.15 kW) | 0.135 PLN |
60W | 200W (0.2 kW) | 0.18 PLN |
100W | 300W (0.3 kW) | 0.27 PLN |
130W | 400W (0.4 kW) | 0.36 PLN |
150W | 450W (0.45 kW) | 0.405 PLN |
Uwaga: Powyższa tabela przedstawia dane szacunkowe i może się różnić w zależności od konkretnego modelu lasera i efektywności systemu chłodzenia.
Eksperckie Oko na Efektywność: Jak Zmniejszyć Koszty Energii
Jak zatem, niczym sprytny strateg, zminimalizować koszty energii elektrycznej związane z pracą lasera CO2? Po pierwsze, zadbaj o efektywność. Używaj lasera tylko wtedy, kiedy jest to konieczne. Wyłączaj go na czas przerw i po zakończeniu pracy. Może to brzmi banalnie, ale uwierz mi, znam przypadki, gdzie lasery pracowały całą noc, "na wszelki wypadek". Po drugie, zainwestuj w energooszczędny system chłodzenia. Nowoczesne chillery potrafią być znacznie bardziej efektywne od starszych modeli. Po trzecie, monitoruj pobór mocy swojego lasera. Miernik zużycia energii, niczym kompas, pomoże Ci zorientować się, gdzie ucieka prąd i jak możesz zoptymalizować proces pracy.
Humorystyczny Akcent na Koniec: Prąd Nie Śpi, Rachunki Też Nie
Na koniec, mała anegdota z życia wzięta. Pewien przedsiębiorca, nazwijmy go panem X, tak bardzo skupił się na precyzji cięcia laserowego, że zupełnie zapomniał o kosztach energii. Dopiero, gdy otrzymał rachunek za prąd, jak grom z jasnego nieba, zdał sobie sprawę, że jego "elektryczny smok" jest prawdziwym pożeraczem pieniędzy. Od tamtej pory, pan X, niczym nawrócony grzesznik, z pietyzmem wyłącza laser po każdej sesji pracy. Pamiętaj, prąd nie śpi, a rachunki za prąd też nie. Mądre zarządzanie kosztami energii to klucz do rentowności i sukcesu w laserowym biznesie. Nie pozwól, aby elektryczny smok zjadł Twój zysk!
Żywotność Tuby Laserowej i Koszty Eksploatacyjne Lasera CO2
Zagłębiając się w temat kosztów godzinowej pracy lasera CO2, nie sposób pominąć kluczowego aspektu, jakim jest żywotność tuby laserowej oraz związane z nią koszty eksploatacyjne. To serce systemu, element, który niczym silnik w samochodzie, napędza całą maszynerię precyzyjnej obróbki materiałów. Podczas gdy początkowa cena zakupu lasera jest istotna, to właśnie długoterminowe koszty, w tym wymiana tuby i bieżąca eksploatacja, decydują o rzeczywistej opłacalności inwestycji. Zatem, przyjrzyjmy się bliżej temu, co kryje się za frazesem "koszt godziny pracy lasera CO2", rozkładając go na czynniki pierwsze.
Różne Typy Tub Laserowych CO2 i Ich Żywotność: Wyścig Technologii
Na rynku w 2025 roku dominują zasadniczo trzy typy tub laserowych CO2, każda z nich oferująca inny profil żywotności i kosztów. Najbardziej rozpowszechnione, choć powoli ustępujące miejsca nowszym rozwiązaniom, są tuby szklane. Można je porównać do niezawodnych, choć nieco przestarzałych, modeli telefonów komórkowych – jeszcze działają, ale konkurencja nie śpi. Ich żywotność, w zależności od producenta i intensywności użytkowania, oscyluje w granicach 1500 do 2500 godzin pracy. Mówimy tu o godzinach realnej emisji wiązki laserowej, a nie całkowitego czasu włączenia urządzenia. Cena nowej tuby szklanej waha się od 300 do 800 PLN, co na pierwszy rzut oka wydaje się kwotą niewielką. Jednakże, jeśli weźmiemy pod lupę częstotliwość wymian, obraz staje się nieco bardziej skomplikowany.
Kolejnym graczem na arenie są tuby metalowe. Te, niczym sportowe samochody w świecie motoryzacji, oferują wyższą wydajność i dłuższą żywotność. Ich konstrukcja, oparta na metalowej obudowie, zapewnia lepsze odprowadzanie ciepła i większą stabilność pracy. Żywotność tub metalowych to już przedział od 4000 do 8000 godzin, co przekłada się na rzadszą konieczność wymiany. Koszt zakupu jest wyższy, bo wynosi od 1500 do 4000 PLN, ale w dłuższej perspektywie, biorąc pod uwagę żywotność, mogą okazać się bardziej ekonomicznym wyborem. Pamiętajmy, czas to pieniądz, a przestoje związane z wymianą tuby generują dodatkowe koszty.
Na szczycie technologicznej piramidy stoją tuby RF (radiowo wzbudzane). To prawdziwe "Ferrari" wśród tub laserowych – najdroższe, ale i najbardziej zaawansowane. Ich żywotność to imponujące 10000 do 20000 godzin, co w praktyce oznacza, że przy standardowym użytkowaniu, tuba może służyć przez wiele lat bez konieczności wymiany. Cena tuby RF to jednak wydatek rzędu 5000 do 15000 PLN. Inwestycja ta zwraca się przede wszystkim w zastosowaniach przemysłowych, gdzie liczy się ciągłość pracy i minimalizacja przestojów. Decyzja o wyborze typu tuby to zatem nie tylko kwestia budżetu początkowego, ale przede wszystkim analiza potrzeb i przewidywanego obciążenia lasera.
Kluczowe Czynniki Wpływające na Żywotność Tuby Laserowej: Diabeł tkwi w szczegółach
Nawet najlepsza tuba laserowa nie osiągnie deklarowanej żywotności, jeśli nie zadbamy o odpowiednie warunki pracy. Podobnie jak silnik samochodu, który zaniedbany, szybko odmówi posłuszeństwa, tak i tuba laserowa wymaga troski i uwagi. Jednym z kluczowych czynników jest moc lasera, z jaką pracujemy. Paradoksalnie, praca na niższych ustawieniach mocy wcale nie musi wydłużyć żywotności tuby. Wręcz przeciwnie, częste rozpalanie i wygaszanie lasera, szczególnie przy intensywnym trybie pracy, może skracać jej żywotność. Złotym środkiem jest optymalne dobranie mocy do zadania, unikając zarówno przeciążania tuby, jak i pracy na zbyt niskich parametrach.
Chłodzenie to kolejny, absolutnie fundamentalny aspekt. Tuba laserowa podczas pracy generuje ciepło, które musi być efektywnie odprowadzane. Zaniedbanie chłodzenia to prosta droga do przegrzania i uszkodzenia tuby. W 2025 roku standardem są systemy chłodzenia wodnego, oparte na chillerach. Należy regularnie kontrolować poziom i jakość płynu chłodzącego, a także dbać o czystość układu. Zanieczyszczenia i osady mogą obniżać efektywność chłodzenia, prowadząc do wzrostu temperatury tuby. Pamiętajmy, przegrzana tuba laserowa to jak przegrzany silnik – awaria jest tylko kwestią czasu.
Czystość optyki to kolejny element układanki. Zanieczyszczone soczewki i lustra absorbują energię lasera, zamiast ją przepuszczać. To nie tylko obniża moc lasera, ale również generuje dodatkowe ciepło, które może uszkodzić tubę. Regularne czyszczenie optyki, zgodnie z zaleceniami producenta, to nie tylko kwestia wydajności, ale również żywotności tuby. Można to porównać do dbania o czystość okien – przez brudne okna światło słabiej wpada, a przez brudną optykę laser traci moc.
Nie można zapomnieć o jakości gazu w tubie. W tubach szklanych gaz jest zazwyczaj zamknięty na stałe, ale w niektórych modelach tub metalowych i RF istnieje możliwość refillu gazu. Utrata szczelności tuby lub zanieczyszczenie gazu to poważne problemy, które mogą znacząco skrócić żywotność. Warto wybierać tuby od renomowanych producentów, którzy gwarantują jakość i szczelność swoich produktów. "Tanie mięso psy jedzą" – przysłowie to doskonale oddaje sytuację z tanimi, niesprawdzonymi tubami laserowymi.
Analiza Kosztów Eksploatacyjnych Lasera CO2: Nie Tylko Tuba, Ale Cała Orkiestra
Koszty eksploatacyjne lasera CO2 to nie tylko wymiana tuby laserowej. To cała gama wydatków, które sumują się w końcowy rachunek za godzinę pracy. Zacznijmy od energii elektrycznej. Laser CO2, szczególnie te o większej mocy, to urządzenie energochłonne. Koszt energii elektrycznej za godzinę pracy, w zależności od mocy lasera i cen prądu w 2025 roku, może wynosić od 0.5 PLN do 2 PLN. Niby niewiele, ale w skali miesiąca czy roku, sumy te mogą być znaczące. Pamiętajmy, "ziarnko do ziarnka, a zbierze się miarka".
Chłodzenie, o którym już wspominaliśmy w kontekście żywotności tuby, to również koszt. Chillery, czyli urządzenia do chłodzenia wodnego, także zużywają energię elektryczną. Dodatkowo, wymagają regularnego przeglądu i konserwacji, co generuje kolejne wydatki. Roczny koszt konserwacji systemu chłodzenia może wynosić od 200 do 500 PLN. Czasem, w ferworze walki o niskie koszty początkowe, zapominamy o kosztach utrzymania, a to błąd.
W przypadku niektórych tub laserowych (choć w 2025 roku to już rzadkość, głównie starsze modele tub metalowych), może pojawić się konieczność refillu gazu. Koszt takiej operacji to wydatek rzędu 500 do 1000 PLN, i choć nie jest to koszt częsty, warto go uwzględnić w kalkulacji. Na szczęście, większość nowoczesnych tub laserowych to konstrukcje szczelne, niewymagające refillu gazu przez cały okres żywotności.
Nie można zapomnieć o materiałach eksploatacyjnych, takich jak soczewki i lustra. Mimo regularnego czyszczenia, z czasem ulegają one zużyciu i wymagają wymiany. Koszt wymiany optyki zależy od jakości i rodzaju komponentów, ale warto przyjąć, że w skali roku, na materiały eksploatacyjne trzeba przeznaczyć kilkaset złotych. "Lepiej zapobiegać niż leczyć" – regularna konserwacja i wymiana zużytych elementów to inwestycja w długotrwałą i bezproblemową pracę lasera.
Na koniec, najbardziej bolesny koszt – koszt przestoju. Awaria tuby laserowej, czy jakikolwiek inny problem techniczny, powoduje zatrzymanie produkcji i generuje straty. Koszt przestoju za godzinę pracy lasera, w zależności od profilu działalności i skali produkcji, może wynosić od 100 do 500 PLN, a nawet więcej. Dlatego tak ważna jest prewencja, regularne przeglądy i dbałość o laser. "Mądry Polak po szkodzie" – ale lepiej być mądrym przed szkodą, i minimalizować ryzyko przestojów.
Kiedy Tuba Mówi "Dość": Symptomy Zużycia i Wymiana, czyli Pogrzeb z Honorami
Jak rozpoznać, że tuba laserowa zbliża się do kresu swojej żywotności? Pierwszym i najbardziej oczywistym sygnałem jest spadek mocy lasera. Materiały, które wcześniej były cięte i grawerowane bez problemu, nagle stają się trudne do obróbki. Parametry, które kiedyś działały idealnie, trzeba korygować, zwiększając moc i spowalniając prędkość. To jak z człowiekiem, który z wiekiem traci siły i wigor.
Kolejnym symptomem jest pogorszenie jakości wiązki laserowej. Linie cięcia stają się mniej precyzyjne, krawędzie poszarpane, grawerunek mniej wyraźny. Czasem można zauważyć, że wiązka laserowa staje się "rozmyta", traci swoją ostrość. To znak, że tuba "daje z siebie wszystko", ale jej dni są policzone.
Czasem tuba laserowa daje znać o swoim zużyciu w sposób bardziej dramatyczny – przestaje działać nagle i niespodziewanie. W takim przypadku, nie pozostaje nic innego, jak wymiana tuby. Proces wymiany, w zależności od modelu lasera, może być mniej lub bardziej skomplikowany. W niektórych maszynach, wymiana tuby to kwestia kilkunastu minut, w innych – wymaga interwencji serwisu. Koszt wymiany tuby to nie tylko cena nowej tuby, ale również koszty robocizny serwisu, jeśli zdecydujemy się na pomoc specjalistów.
Wymiana tuby laserowej to nieunikniony element eksploatacji lasera CO2. Traktujmy to jak wymianę opon w samochodzie – nie jest to przyjemne, ale konieczne, aby maszyna mogła dalej sprawnie działać. Po wymianie tuby, laser odzyskuje swoją dawną moc i precyzję, i możemy dalej cieszyć się jego możliwościami. "Stara miłość nie rdzewieje" – ale czasem trzeba ją odświeżyć, wymieniając zużyte elementy.
Długoterminowa Perspektywa: Inwestycja w Laser CO2 a Koszty Przyszłe, czyli Myśl o Jutrze
Decydując się na zakup lasera CO2, warto spojrzeć na inwestycję z długoterminowej perspektywy. Nie tylko cena zakupu, ale przede wszystkim koszty eksploatacyjne i żywotność tuby laserowej, decydują o rzeczywistej opłacalności. Wybierając tubę laserową, warto zastanowić się nad intensywnością użytkowania lasera. Jeśli planujemy pracę w trybie ciągłym, inwestycja w droższą, ale żywotniejszą tubę metalową lub RF, może okazać się bardziej opłacalna w dłuższej perspektywie. "Co tanie to drogie" – przysłowie to idealnie pasuje do sytuacji, gdy oszczędzając na tubie, narażamy się na częste wymiany i przestoje.
Prewencyjna konserwacja i dbałość o laser, to klucz do minimalizacji kosztów eksploatacyjnych i wydłużenia żywotności tuby laserowej. Regularne czyszczenie optyki, kontrola układu chłodzenia, unikanie pracy na ekstremalnych parametrach – to proste czynności, które mogą znacząco wpłynąć na żywotność i bezawaryjność lasera. "Kto rano wstaje, temu Pan Bóg daje" – a w naszym przypadku, "kto dba o laser, ten dłużej pracuje".
Podsumowując, koszt godziny pracy lasera CO2 to wypadkowa wielu czynników. Żywotność tuby laserowej i koszty jej wymiany, energia elektryczna, materiały eksploatacyjne, konserwacja, i potencjalne koszty przestojów – wszystko to składa się na końcowy rachunek. Dokładna analiza tych kosztów, i świadomy wybór typu tuby laserowej, to klucz do optymalizacji wydatków i maksymalizacji zysków z inwestycji w technologię laserową. "Liczmy koszty, a będziemy bogaci" – to motto, które warto zapamiętać, planując eksploatację lasera CO2.
Jak Moc Lasera CO2 Wpływa na Koszt Godziny Pracy?
Kwestia kosztów operacyjnych lasera CO2 to zagadnienie, które spędza sen z powiek niejednemu przedsiębiorcy. Gdy wgryzamy się w temat "Ile kosztuje godzina pracy lasera CO2", szybko odkrywamy, że odpowiedź nie jest tak prosta, jak mogłoby się wydawać. To nie jest tylko cena prądu i amortyzacji. W rzeczywistości, kluczowym, choć często niedocenianym, czynnikiem determinującym koszty jest moc lasera. Zrozumienie tej zależności to jak rozszyfrowanie tajemnego kodu, który otwiera drzwi do optymalizacji wydatków i zwiększenia rentowności.
Inwestycja Początkowa: Moc Mówi Sama Za Siebie
Zacznijmy od przysłowiowego "wejścia smoka" – ceny zakupu urządzenia. Logika jest tutaj brutalnie prosta: im większa moc lasera, tym wyższa cena zakupu. W 2025 roku, laser CO2 o mocy 100W to wydatek rzędu, powiedzmy, 30 000 – 50 000 euro. Przeskakując na wyższą półkę, laser 400W to już inwestycja oscylująca między 80 000 a 150 000 euro. A jeśli marzy nam się potężny 1kW "potwór"? Przygotujmy się na wydatek przekraczający 200 000 euro, a często i znacznie więcej. To jak wybór samochodu – mały, miejski hatchback będzie tańszy niż sportowy SUV z silnikiem V8. Różnica w cenie zakupu bezpośrednio przekłada się na wyższą amortyzację w koszcie godziny pracy.
Koszty Eksploatacji: Energia, Gazy i Serwis – Trójca Święta Wydatków
Ale zakup to dopiero początek. Prawdziwa zabawa zaczyna się, gdy laser rusza do pracy. Tutaj w grę wchodzą koszty eksploatacyjne, które są niczym niekończąca się rzeka wydatków. Moc lasera ma bezpośredni wpływ na zużycie energii elektrycznej. Laser 100W "pociągnie" z sieci powiedzmy 1-2kW na godzinę, podczas gdy 400W może już konsumować 4-6kW. 1kW? Przygotujmy się na 8-12kW. Przyjmując średni koszt energii elektrycznej dla przemysłu w 2025 roku na poziomie 0,15 euro za kWh, łatwo policzyć, że godzinna praca lasera 100W to koszt rzędu 0,15 – 0,30 euro tylko za prąd. Dla 1kW to już 1,2 – 1,8 euro! Różnica robi się znacząca, prawda? To jak porównanie rachunku za prąd w kawalerce i wielkim domu z klimatyzacją działającą non-stop.
Nie zapominajmy o gazach. Lasery CO2, jak sama nazwa wskazuje, wykorzystują mieszankę gazów, w tym dwutlenek węgla, azot i hel. Im większa moc lasera, tym większe zużycie gazów, choć tutaj wpływ nie jest już tak liniowy jak w przypadku energii. Częstotliwość wymiany gazów zależy od intensywności pracy, rodzaju materiału i ustawień. Jednak generalnie, mocniejszy laser, pracujący na pełnych obrotach, będzie wymagał częstszej wymiany lub uzupełniania gazów, co oczywiście generuje dodatkowe koszty.
Serwis i konserwacja to kolejny element układanki. Lasery CO2 to precyzyjne urządzenia, które wymagają regularnych przeglądów i konserwacji. Im bardziej zaawansowana technologia, im większa moc lasera, tym potencjalnie bardziej skomplikowany i kosztowny serwis. Wymiana optyki, czyszczenie i kalibracja – to wszystko kosztuje. Wyższa moc lasera to często większe obciążenie dla komponentów, co może przekładać się na częstsze awarie i krótszą żywotność niektórych podzespołów. To jak z samochodem – sportowe auto, eksploatowane na torze, będzie wymagało częstszych wizyt w warsztacie niż rodzinny sedan.
Czas to Pieniądz: Moc a Wydajność Pracy
Ale chwileczkę! Czy wyższa moc lasera to tylko wyższe koszty? Absolutnie nie! Tutaj dochodzimy do sedna sprawy – wydajności. Moc lasera ma kluczowy wpływ na szybkość i efektywność cięcia i grawerowania. Laser o większej mocy może pracować szybciej, przecinać grubsze materiały i realizować bardziej złożone projekty w krótszym czasie. To jak porównanie ręcznego piły i elektrycznej pilarki łańcuchowej. Ręczna piła jest tania, ale praca nią trwa wieki. Pilarka łańcuchowa jest droższa, ale praca idzie błyskawicznie.
Wyobraźmy sobie, że musimy wyciąć 1000 elementów z pleksi o grubości 10mm. Laser 100W będzie "męczył się" z tym zadaniem, być może potrzebując na jeden element 10 minut. Laser 400W? Może poradzić sobie z tym samym elementem w 3 minuty. A 1kW? Prawdopodobnie w minutę lub nawet szybciej. W przeliczeniu na 1000 elementów, laser 100W będzie pracował ponad 166 godzin, 400W – 50 godzin, a 1kW – tylko 16 godzin! Czas pracy drastycznie spada wraz ze wzrostem mocy.
A co z kosztami pracy operatora? Godzina pracy operatora lasera CO2 to koszt stały, niezależny od mocy urządzenia (powiedzmy, 20 euro za godzinę w 2025 roku). Im krócej trwa proces obróbki, tym mniej godzin pracy operatora musimy zapłacić na wyprodukowanie danej ilości elementów. W naszym przykładzie, dla 1000 elementów, koszt pracy operatora dla lasera 100W wyniesie 3320 euro, dla 400W – 1000 euro, a dla 1kW – tylko 320 euro! Różnica jest kolosalna!
Optymalizacja Kosztów: Balans Mocy i Potrzeb
Wniosek? Moc lasera CO2 to miecz obosieczny. Z jednej strony, wyższa moc to wyższa cena zakupu, wyższe koszty energii i potencjalnie serwisu. Z drugiej strony, wyższa moc to znacznie większa wydajność, krótszy czas pracy i niższe koszty pracy operatora na jednostkę produktu. Kluczem do optymalizacji kosztów jest znalezienie balansu między mocą lasera a rzeczywistymi potrzebami produkcyjnymi. Nie zawsze "więcej mocy" znaczy "lepiej" i "taniej" w długoterminowej perspektywie.
Jeśli nasza produkcja opiera się głównie na cienkich materiałach i prostych projektach, laser 100W może być w zupełności wystarczający i ekonomicznie uzasadniony. Inwestowanie w potężny laser 1kW byłoby w tym przypadku jak kupowanie Ferrari, żeby jeździć nim tylko po mieście w korkach. Z drugiej strony, jeśli specjalizujemy się w cięciu grubych materiałów, grawerowaniu na dużą skalę i zależy nam na wysokiej przepustowości, laser o wyższej mocy będzie niezbędny, aby sprostać wymaganiom rynku i utrzymać konkurencyjność. To jak wybór narzędzi dla rzemieślnika – stolarz nie będzie używał młotka pneumatycznego do wbijania małych gwoździ, a cieśla nie zbuduje domu z samym śrubokrętem.
Podsumowując, aby precyzyjnie odpowiedzieć na pytanie "Jak moc lasera CO2 wpływa na koszt godziny pracy?", musimy przeprowadzić dogłębną analizę naszych potrzeb produkcyjnych, rodzaju obrabianych materiałów, pożądanej przepustowości i budżetu. Kalkulacja kosztów powinna uwzględniać nie tylko cenę zakupu i eksploatacji, ale przede wszystkim wpływ mocy na wydajność i całkowity koszt wytworzenia jednostki produktu. Tylko wtedy będziemy mogli podjąć świadomą decyzję i wybrać laser CO2, który będzie pracował dla nas, a nie my dla niego.